Zinc Die Casting
Zinc die casting is widely favored for its exceptional characteristics, making it an ideal choice for manufacturing intricate and high-precision components. The process allows for complex shapes and thin walls, providing designers and engineers with the freedom to create innovative products. Furthermore, zinc’s excellent casting fluidity ensures intricate details are accurately reproduced, while its corrosion resistance enhances the longevity and durability of the final components.
BIAN DIECAST Zinc die casting / Zinc alloy cast is a die process by using hot chamber machines to inject or shot Zinc materials like zinc#3-5 hot molten metal into shot chamber. As the injection plunger rises, a port in the feed system opens and hot molten metal fills the cylinder. The plunger then moves down, sealing the port and forcing the molten metal through the gooseneck and into the die cavity. After the zinc solidifies, the plunger retracts and the casting is ejected.then we get the product just half finished, later we will get rid of all the Metal Saver,polishing or ultrasonic cleaning,then painting or spraying it to make the last step finished.
The product characteristics of zinc alloy die castings are as follows:
1. Worklife, hardness, texture and strength are much better compared with plastic injection molding.
2. It has good casting performance. It can die cast precision parts with complex shape and thin wall, and the casting surface is smooth.
3. Surface treatment: electroplating, spraying and painting.
4. In the process of smelting and die-casting, there is no iron absorption, corrosion forming, and mold sticking.
5. It has good mechanical properties and wear resistance at room temperature.
6. Low melting point, melting point 385 ℃, easier to form than aluminum alloy die casting.
7. Zinc alloy has a strong three-dimensional sense. There will be grain or wrinkle on the surface after die casting, which needs polishing. Grinding cannot completely change the physical form.
8. Zinc alloy handicrafts and relief patterns are vivid and widely used, but require a high level of technology, with a small amount of indentation or burr on the surface.
Why is zinc used for die casting?
Zinc is commonly used for die casting because of its unique combination of properties that make it highly suitable for this manufacturing process. Here are some key reasons:
1. Excellent Casting Properties
Fluidity: Zinc alloys have excellent fluidity, which allows them to fill complex molds with intricate details, leading to high-precision parts.
Low Melting Point: Zinc has a relatively low melting point (about 419.5°C or 787.1°F), which makes the die casting process more energy-efficient and less taxing on molds and equipment.
2. Durability and Strength
High Impact Strength: Zinc alloys are known for their toughness, making them ideal for components that require durability.
Good Mechanical Properties: Zinc offers a good balance of strength, hardness, and ductility, making it suitable for parts that need to withstand mechanical stress.
3. Cost-Effectiveness
Material Costs: Zinc is relatively inexpensive compared to other metals like aluminum or copper, making it a cost-effective choice for large-scale production.
Recyclability: Zinc is highly recyclable, reducing waste and contributing to cost savings in manufacturing.
4. Dimensional Stability
Minimal Shrinkage: Zinc alloys exhibit low shrinkage during solidification, ensuring that cast parts maintain their intended dimensions and reducing the need for additional machining.
5. Corrosion Resistance
Zinc alloys offer good corrosion resistance, which is especially beneficial for components exposed to harsh environments.
6. Surface Finish
Zinc die castings can achieve a high-quality surface finish, allowing for easy plating, painting, or other surface treatments, enhancing the aesthetic appeal and functionality of the final product.
7. Shorter Cycle Times
Due to the quick cooling and solidification of zinc alloys, the die casting process can have shorter cycle times, increasing production efficiency.
These attributes make zinc an ideal material for producing a wide variety of components, from small precision parts to larger, more robust pieces, commonly found in industries such as automotive, electronics, and hardware.
What are the differences between zinc alloy die casting and aluminum alloy die casting?
There are many die-casting processes in die-casting manufacturers, of which zinc alloy die-casting and aluminum alloy die-casting take almost 80% of the market. Zinc alloy in zinc alloy die-casting is an alloy based on zinc and added with other elements.
Commonly added alloy elements include aluminum, copper, magnesium, cadmium, lead, titanium and other low-temperature zinc alloys. Compared to Aluminum cast, Zinc alloy has low melting point, good fluidity, easy fusion welding, brazing and plastic processing, corrosion resistance in the atmosphere, and easy recovery and remelting of residual waste; However, the creep strength is low and the size change is easily caused by natural aging. Prepared by melting method, die-casting or pressure processing.
According to the manufacturing process, it can be divided into cast zinc alloy and deformed zinc alloy. It can be used for die-casting instruments, automobile parts, electric pole surface galvanizing and anti-corrosion, boiler water wall pipe hot-dip galvanizing to improve high-temperature corrosion resistance, etc.
Zinc die casting has become a preferred choice for manufacturing intricate and high-precision components across various industries. As a cost-effective and versatile process, it allows for the creation of complex shapes and thin-walled parts with exceptional dimensional accuracy. The process involves injecting molten zinc into dies under high pressure, resulting in sturdy and precise components that meet stringent quality standards.
Why BIAN is Recognized as a Leading Zinc Die Casting Factory in China
1. Advanced Manufacturing Capabilities
As one of the leading Die casting factories, BIAN Die Casting specializes in high-precision zinc die casting using state-of-the-art equipment, including automated die casting machines and CNC machining centers. Their focus on thin-wall zinc casting and multi-slide die casting enables them to produce complex, lightweight components with tolerances as tight as ±0.02mm. This capability is critical for industries like automotive, electronics, and consumer goods, where precision is non-negotiable.
2. Rigorous Quality Control Systems
The factory adheres to ISO 9001 and IATF 16949 certifications, ensuring compliance with global automotive quality standards. Every zinc die casting component undergoes:
– Material composition analysis (e.g., Zamak alloys).
– Dimensional inspection via 3D CMM (Coordinate Measuring Machines).
– Pressure testing and surface finish evaluations.
This meticulous process minimizes defects and ensures long-term durability.
3. Custom Solutions for Diverse Industries
BIAN serves clients across high-demand sectors:
Automotive: Zinc alloy parts for connectors, housings, and sensors.
Electronics: EMI/RFI shielding components and heat sinks.
Consumer Goods: Decorative hardware and precision fittings.
Their ability to customize designs (e.g., textured finishes, electroplating) aligns with branding and functional requirements.
4. Sustainable Production Practices
BIAN prioritizes eco-friendly manufacturing:
Recyclable Zinc Alloys: 95%+ of scrap zinc is reused.
Energy-Efficient Processes: Reduced carbon footprint through optimized furnace operations.
Waste Reduction: Closed-loop cooling systems and lean production workflows.
5. Global Client Trust and Industry Recognition
BIAN has partnered with Fortune 500 companies and SMEs worldwide, earning acclaim for:
On-Time Delivery: 98%+ fulfillment rate.
Cost Efficiency: Competitive pricing through scaled production.
Technical Support: Dedicated engineering teams for prototyping and material selection.
BIAN Die Casting’s combination of precision engineering, quality assurance, customization, and sustainability solidifies its position as a top-tier zinc die casting factory in China. For businesses seeking reliable, high-performance zinc alloy components, BIAN’s expertise and client-centric approach make it a standout choice.
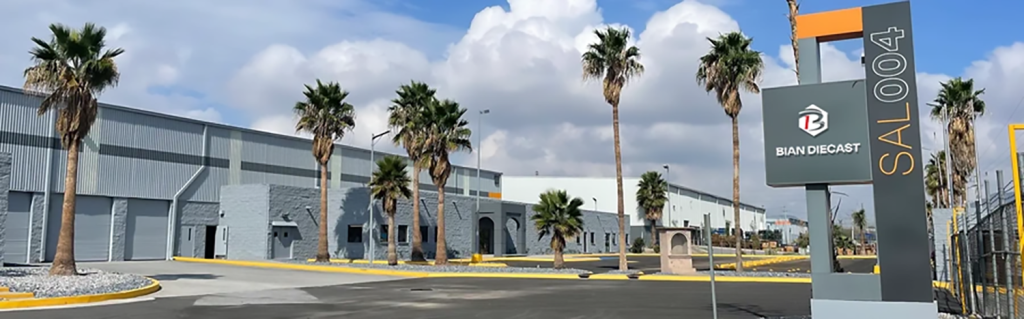