Die Casting Mold: Design Principles, Applications & Top Manufacturer in China | BIAN METAL
In the fast-evolving landscape of industrial production, die casting molds stand as the backbone of mass-producing complex metal components with micron-level accuracy. These molds enable industries to achieve cost efficiency, repeatability, and structural integrity across sectors like automotive, aerospace, and consumer electronics. This article unpacks the science behind die casting molds, their strategic applications, and criteria for selecting a reliable supplier, with a spotlight on BIAN METAL, a trailblazer in China’s die casting mold industry.
What is a Die Casting Mold?
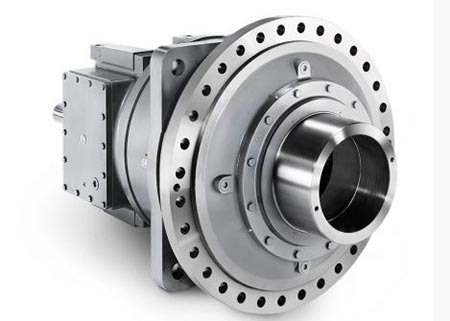
A die casting mold is a high-strength steel tool engineered to shape molten metal (e.g., aluminum, zinc, or magnesium alloys) under extreme pressure. It comprises two primary halves – the fixed “cover die” and the movable “ejector die” – that form a cavity replicating the final part’s geometry. Key characteristics include:
– Material Durability: H13 hot-work steel or maraging steel for thermal fatigue resistance.
– Cooling Systems: Integrated channels to regulate temperature and reduce cycle times.
– Surface Treatments: Nitriding or chromium plating to prevent corrosion and wear.
Advantages of Advanced Die Casting Molds
Modern die casting molds offer transformative benefits for manufacturers:
– Precision: Tolerances as tight as ±0.02 mm for critical components like engine blocks.
– Cost Efficiency: High-volume production reduces per-unit costs by up to 60%.
– Sustainability: Reusable molds minimize material waste versus sand casting.
– Speed: Cycle times as low as 15 seconds for small parts in automotive applications.
Industry Applications of Die Casting Molds
Die casting molds are indispensable across sectors demanding lightweight and durable metal parts:
– Automotive: Engine brackets, transmission housings, and EV battery trays.
– Consumer Electronics: Heat sinks for smartphones and laptop chassis.
– Aerospace: Lightweight components for satellites and aircraft actuators.
– Medical Devices: Sterilizable surgical instrument housings.
BIAN METAL: China‘s Premier Die Casting Mold Manufacturer
BIAN METAL has carved a niche as a global leader in die casting mold production, combining German-engineered CNC machining with localized cost efficiency.
Why Partner with BIAN METAL?
Technical Expertise:
– Simulation-Driven Design: Uses MAGMASOFT® to predict flow defects and optimize cooling.
– Multi-Slide Molds: Capable of producing undercuts and complex geometries.
Quality Assurance:
– ISO 9001-certified processes with 3D scanning for dimensional verification.
– Hardness testing (HRC 48–52) to ensure mold longevity.
– Global Clientele: Supplies molds to Tesla, Siemens, and Bosch.
Case Study: A European EV manufacturer reduced part rejection rates by 95% using BIAN METAL’s AI-optimized aluminum die casting molds.
Key Considerations When Selecting a Die Casting Mold
To maximize ROI, evaluate suppliers based on:
– Material Compatibility: Expertise in your alloy (e.g., ADC12 aluminum vs. ZAMAK zinc).
– Tool Life: Guaranteed lifespan (e.g., 150,000+ cycles for H13 steel molds).
– Post-Processing: Capabilities like trimming, deburring, and T6 heat treatment.
– Lead Times: Rapid prototyping options (e.g., 30-day turnaround for pilot molds).
Future Trends in Die Casting Mold Technology
Innovations reshaping the industry include:
– AI-Powered Predictive Maintenance: Sensors detect mold wear in real-time, reducing downtime.
– Hybrid Additive Manufacturing: 3D-printed conformal cooling channels for faster cycle times.
– Eco-Friendly Materials: Recyclable steel alloys and low-carbon production processes.
Conclusion
Die casting molds are pivotal to achieving precision, efficiency, and scalability in metal component manufacturing. By collaborating with BIAN METAL, businesses gain access to cutting-edge mold technology backed by rigorous quality controls and industry-specific expertise. As industries push toward lightweighting and sustainability, advanced die casting molds will remain a cornerstone of innovation.