China Die Casting Manufacturers: Shaping the Future of Precision Manufacturing
As of February 27, 2025, China remains the epicenter of global die casting production, accounting for over 40% of the world’s market share. With industries like electric vehicles (EVs), aerospace, and consumer electronics demanding lightweight, complex metal components, Chinese die casting manufacturer are redefining precision, scalability, and sustainability. This article delves into the strengths of China die casting sector, emerging technologies, and highlights BIAN METAL—a trailblazer in the field.
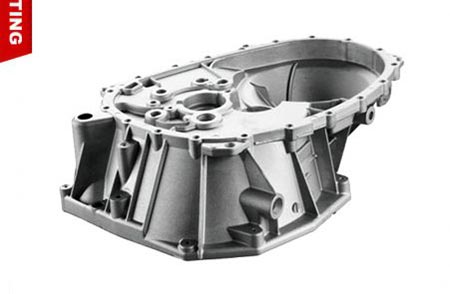
Why China Dominates Die Casting Manufacturing
China die casting industry thrives on a unique blend of cost efficiency, technological innovation, and supply chain integration. Key advantages include:
– Cost-Effective Production: Competitive labor and raw material costs enable 30–50% savings compared to Western counterparts.
– Advanced Automation: Over 75% of top-tier factories now integrate AI-driven quality control and robotic systems for high-volume output.
– End-to-End Solutions: From mold design to post-processing (e.g., CNC machining, surface coating), Chinese manufacturers offer vertical integration.
– Sustainable Practices: Adoption of recycled aluminum alloys and closed-loop water systems aligns with global ESG standards.
Key Technologies Revolutionizing Die Casting in 2025
A. High-Pressure Die Casting (HPDC)
– Ultra-Thin Wall Casting: Producing components as thin as 0.6 mm for EVs and 5G devices.
– Vacuum-Assisted Casting: Minimizes porosity in critical parts like battery housings and structural frames.
B. Smart Factories
– Digital Twin Systems: Simulating mold designs and process parameters to reduce trial cycles by 60%.
– IoT-Enabled Monitoring: Real-time tracking of temperature, pressure, and cycle times to optimize yield rates.
C. Material Innovations
– Silicon-Aluminum Alloys: Enhanced thermal conductivity for EV power electronics.
– Magnesium Alloys: Lightweight alternatives for aerospace applications.
Applications Driving Demand for China Die Casting
– Electric Vehicles: Battery enclosures, motor housings, and charging ports.
– Consumer Electronics: Heat sinks for 5G infrastructure, smartphone frames.
– Industrial Machinery: Hydraulic valve blocks, pump components.
– Renewable Energy: Wind turbine gearbox housings and solar panel brackets.
Challenges and Solutions for Chinese Manufacturers
Key Challenges
– Global Tariff Pressures: Navigating trade barriers in the EU and North America.
– Energy Transition: Reducing reliance on coal-powered furnaces.
– Skill Gaps: Training technicians in AI and advanced metallurgy.
Strategic Responses
– Nearshoring Facilities: Establishing plants in Mexico and Eastern Europe to bypass tariffs.
– Green Energy Adoption: Transitioning to solar and hydrogen-based melting systems.
– Industry-Academia Partnerships: Collaborating with universities to upskill workforce.
BIAN METAL: A Leader in China Die Casting Industry
BIAN METAL exemplifies China manufacturing prowess with its focus on precision, innovation, and sustainability:
Core Competencies
– Precision Engineering: Tolerances as tight as ±0.02 mm for medical and aerospace components.
– Global Certifications: IATF 16949 for automotive quality, ISO 13485 for medical devices.
– Custom Solutions: Prototype-to-mass-production support for niche industries like robotics and defense.
Product Portfolio
– Aluminum Die Casting: High-strength parts for EVs and IoT devices.
– Zinc Alloy Casting: Decorative hardware and consumer electronics.
– Multi-Material Hybrid Casting: Combining metals and polymers for weight-critical applications.
Sustainability Leadership
– Zero-Waste Foundries: Recycling 98% of scrap metal and using biodegradable release agents.
– Carbon-Neutral Roadmap: Aiming for net-zero emissions by 2030 through renewable energy partnerships.
Future Trends in Die Casting (2025–2030)
– AI-Driven Process Optimization: Predictive maintenance and defect detection.
– 3D-Printed Molds: Reducing lead times for complex geometries by 50%.
– Cross-Industry Synergies: Adopting aerospace-grade standards for automotive parts.
Conclusion
China die casting manufacturer, led by innovators like BIAN METAL, are pivotal to the global shift toward lightweight, high-performance metal components. By leveraging automation, sustainable practices, and R&D investments, BIAN METAL delivers solutions that meet the stringent demands of industries ranging from EVs to renewable energy.
For tailored die casting solutions, visit www.biandiecast.com or connect with their engineering team to discuss your project requirements.