Aluminum Die Casting
(1) The liquid metal is filled with the cavity under pressure, and crystallizes and solidifies under higher pressure, the common pressure is 15-100mpa.
(2) Molten aluminum to be quicly filled in cavity at high speed, usually in 10-50 m/s, some can be more than 80 m/s, (through the gate into the cavity linear velocity – gate speed), so the filling time of liquid metal is very short, about 0.01-0.2 seconds (depending on the size of the casting and different) can be filled cavity. Die casting machine, die casting alloy and die casting die are the three main elements of die casting production. The so-called die casting process is the organic comprehensive use of these three elements, so that the appearance, internal quality, good size in line with the drawing or agreement requirements of qualified castings, and even high quality castings can be produced steadily and rhythmically.
(3) BIAN provide different customization aluminum die casting parts and components for all kinds of industries including LED Lights Housing, Automative Part, Electronic Part, Medical Components, Kitchen Utensils, Furniture Part, Architectural /Building Hardware etc. with an annual output of more than 2000molds and countless parts for the above mentioned industries.
(4) Cast aluminum industry extremely depends on experience and technical strength, so what BIAN DIECAST have ?
a. More than 10 years of experience in mold design and manufacturing.
b. Experienced mold engineering & technicians technicians and mold manufacturing operators.
c. Mold flow analysis and Mold casting system simulation analysis software: Cast-Designer, etc., continuously optimize the structure of the mold according to the results of mold flow analysis,
d. We have one-stop full set process of your die cast products as well as relatived equiments like CNC Mold Machines, drilling/turning machines, LASER cutting, annealing equipemt, EDM machines, polish machine, Automatic painting line, and full set of testing device like CMM machine, size detector, X-ray detector, salt spray tester and so on.
(5) Introduction to the liquidity of BIAN aluminum alloy die casting:
Fluidity refers to the ability of the alloy liquid to fill the mold. The fluidity determines whether the alloy can cast complex castings. The liquidity of eutectic alloy in aluminum alloy die casting is the best. There are many factors that affect the fluidity, mainly the composition, temperature and solid particles of metal oxides, metal compounds and other pollutants in the alloy liquid, but for BIAN, we will choose the best fluidity material usually like ADC12, a360, A380 or En44300 etc .. According the usage and other features of different final products from our customers.
ALUMINUM DIE CASTING
Why Pick the Best Aluminum Die Casting Manufacturer Now?
Having die-casting aluminum projecting is a manageable errand. Naturally, some research is required to simplify it, and investing is not bad. Of course, it fulfills eligible industrial purposes, as anticipated. It should go through something special and have an immediate coin or bullion. You have to prefer us forever and designs ought to accompany the investments. It will create a superior one and investigate metal dealers’ bullion bars. To meet casting requirements, it ought to make products more flexible forever. For various reasons, it would be helpful if you knew Bian Die Cast, a professional company focusing on high-end casting of die accordingly.
Direct Investment in Aluminum
Naturally, the entire procedure takes a short time to investigate new direct purchase options. As a result, the project should have more options and be able to concentrate on direct casting. It gains exposure to the value of it and takes a complete pledge solution, depending on the aluminum die casting manufacturer. It must adjust to focus on high-end, beneficial solutions. The pass on projecting speculation should remain ongoing and everlastingly incorporate metal sellers. The cycle should go through unambiguous arrangements and put straightforwardly in project requirements. It needs to be practical enough to measure values and used for investing. They change a lot and tend to focus primarily on high-end outcomes.
Aluminum Die Casting Manufacturer
What is the aluminium die casting process?
Aluminum die casting is a manufacturing process where molten aluminum is injected into a steel mold or die under high pressure. The process is widely used for creating complex, precise metal parts with excellent surface finishes and dimensional accuracy. Here’s a breakdown of the aluminum die casting process:
1. Preparation of the Die:
The die, usually made of high-grade steel, consists of two halves: the cover die half and the ejector die half.
These dies are designed to create the desired shape of the final part and include channels for the aluminum to flow and cooling systems to manage the temperature during casting.
2. Melting the Aluminum:
Aluminum ingots or scrap aluminum are melted in a furnace until they reach a liquid state, usually at temperatures around 660°C (1220°F).
3. Injection:
The molten aluminum is then injected into the die cavity using a hydraulic piston. The injection is done under high pressure, typically ranging from 1,500 to 25,000 psi, ensuring that the molten metal fills all the intricate details of the die.
4. Cooling and Solidification:
Once the die is filled, the aluminum begins to cool and solidify. The cooling time varies depending on the size and complexity of the part.
The die may be equipped with cooling channels that circulate water or oil to accelerate the cooling process.
5. Ejection:
After the aluminum has solidified, the die is opened, and the finished part is ejected using ejector pins.
The part may have some excess material, such as runners or flash, which is later trimmed off.
6. Finishing:
The cast parts may undergo additional finishing processes such as trimming, sanding, or machining to achieve the desired specifications.
Surface treatments like painting, powder coating, or anodizing can be applied for added protection and aesthetics.
7. Quality Control:
The parts are inspected for defects such as porosity, cracks, or incomplete filling. Any defective parts are either reworked or scrapped.
Advantages of Aluminum Die Casting:
High Precision: Aluminum die casting allows for the production of highly detailed and dimensionally accurate parts, making it ideal for complex designs.
Lightweight: Aluminum is significantly lighter than other metals like steel, making it suitable for applications where weight is a critical factor.
Durability: Parts produced through this method exhibit excellent strength and resistance to corrosion, making them durable in various environments.
Cost-Effective for High Volumes: The process is highly efficient for mass production, with low per-unit costs for large quantities of parts.
Excellent Surface Finish: The process can achieve smooth surfaces, reducing the need for additional finishing processes.
Applications of Aluminum Die Casting:
Aluminum die casting is used in numerous industries to produce a wide range of components, including:
Automotive Parts: Engine blocks, transmission cases, and structural components.
Aerospace Components: Lightweight, strong parts for aircraft.
Consumer Electronics: Housings for smartphones, laptops, and other devices.
Industrial Machinery: Components for various types of equipment.
Aluminum die casting technology is a versatile and efficient manufacturing process that plays a crucial role in producing high-quality metal parts for a wide array of industries. Its ability to create complex shapes with precision, while maintaining the strength and lightweight properties of aluminum, makes it an invaluable technology in modern manufacturing.
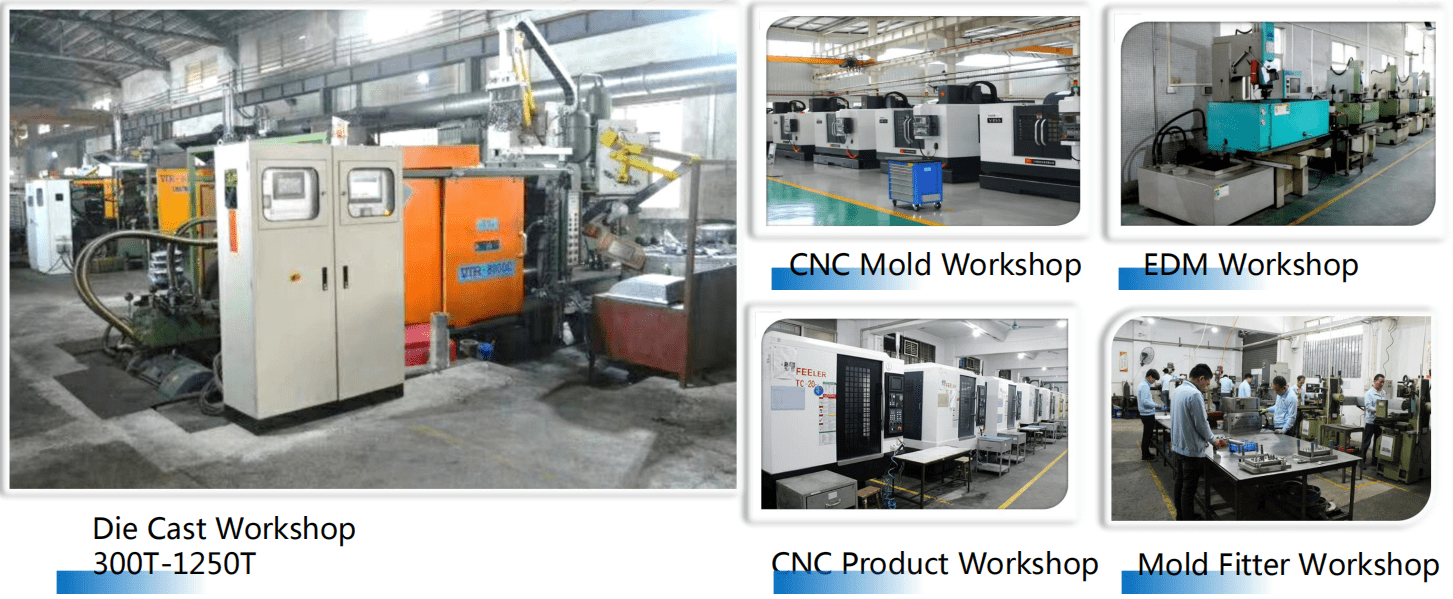
Learn more:
The application of aluminum die casting services in recent decades
The Marvels of Aluminum Die Casting: Unleashing Versatility and Efficiency
Aluminum Die Casting vs Zinc Die Casting
What is the most common die cast aluminum?
How much does aluminum casting tooling cost?
What grade of aluminum is used for die cast?
What is the best aluminum for die casting?