About the process of BIAN aluminum die cast parts
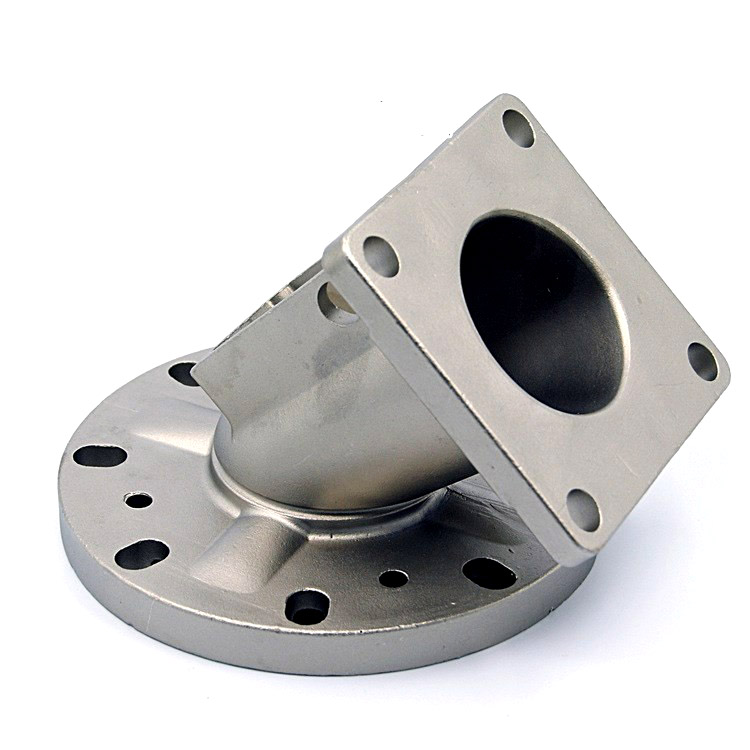
Aluminum die casting is a manufacturing process that involves injecting molten aluminum into a steel die under high pressure, resulting in a high-quality, precise product. This process can be used to create a wide range of aluminum parts, from engine parts to consumer electronics.
The process of aluminum die casting can be broken down into several steps. Here’s how it works:
1. Melting the AluminumAlloy normally in BIAN we use ADC12,ADC6,A360,A380 aluminum: The first step is to melt the aluminum. Raw aluminum ingots are melted down in a furnace to become molten aluminum. The temperature is generally between 650°C to 690°C.
2. Injection the molten aluminum alloy: Once the aluminum is molten, a high-pressure injection machine is used to inject the molten aluminum into the steel die. This die casting machines will ensure that the molten aluminum fills the mold with the correct dimensions, shapes, sturdiness and weight.
3. Press and Solidification: Once the mold cavity is filled, the aluminum is pressed by 180T TO 1250T power rapidly and then fast cooled, the temperature of the aluminum drops quickly. As a result, it solidifies into the desired shape.
4. Ejection: After the part cools down, the die is opened, and the part is ejected. It is then inspected for any defects or inaccuracies.
5. Finishing: The part may require additional finishing processes. Processes such as sanding, polishing, and painting can be applied to give the part its final look and finish.
In addition to providing high-quality aluminum parts, aluminum die casting has several advantages over other casting processes. It is more cost-effective than other methods because the production can happen at a faster rate. There are also fewer materials that go to waste. Aluminum parts produced through this process are lightweight, have high dimensional stability, and can be produced in intricate shapes.
Overall, aluminum die casting is an efficient and reliable process for producing high-quality aluminum parts with excellent dimensional accuracy and consistency. It’s no wonder that it’s a popular choice for manufacturers of all kinds of products.